爱普生晶体设备的历史
晶体设备悄悄地记录着时间的流逝,从电视到电脑和手表,无所不包。它们已经成为电子行业不可或缺的固定装置,以至于日本人称它们为“工业之盐”。作为晶体设备的领先制造商,爱普生不断推动设备节能、小型化和性能的进步。爱普生用“省、小、精技术”这个词来概括其创新理念。这种方法植根于爱普生DNA 中。它使我们能够继续开发更小、功耗更低、性能更卓越的设备。这是爱普生晶体设备的简史。
- 1891
- 前身Yoshimura Shokai成立。
- 1938
- 继承Yoshimura Shokai的Toyo Wireless Telegraph and Telephone与Meisho Electric合并,成立了Toyo Communication Equipment Co., Ltd。
- 1942
- 精工爱普生的前身Daiwa Kogyo, Ltd.成立。
- 1943
- Daini Seikosha(K.Hattori & Co.)手表制造部门成立。
该工厂位于长野县诹访市,是为了躲避第二次世界大战的空袭而建立的。 - 1959
-
日本首次培育出工业合成晶体
当时,人们正在加工大块、高品质、杂质少的天然石英晶体以供使用,但这种晶体在国内很难获得,因为当时石英在世界各地被用作军事材料。因此,我们着手独立生产大块、高品质的合成晶体。首先,我们需要生产高压釜并对其进行微调,以制造高品质的合成晶体。然后,我们增加了更多的高压釜,以进行量产。这使我们能够成功地在日本以工业规模培育出第一批合成晶体。 - Daini Seikosha's Suwa factory与Daiwa Kogyo合并,成立Suwa Seikosha。
- 1969
-
开发世界上第一款商用石英腕表
世界上第一款石英表 Seiko Quartz Astron 35SQ
晶体单元尺寸比较
(左)Quartz Astron 开发之前投入实际使用的晶体单元(约 50 毫米长)。
(中)Quartz Astron 中使用的音叉晶体单元(直径 4.3 毫米 x 长度 18.5 毫米)在世界上第一块石英手表开发之前,存在极其精确的石英手表,但只有挂钟那么大,不容易运输。世界上第一款石英腕表 Seiko Quartz Astron 35SQ 的实用之处在于其准确性和小巧的尺寸。Astron 的精确度达到惊人的每天 ±0.2 秒,是通过将晶体单元、手表 IC 和超紧凑型步进电机技术相结合实现的。创建手表需要将晶体单元小型化。传统的晶体谐振器太大,无法放入手表中。这个问题通过使用新的音叉型结构得到了解决。Cal. 35SQ 机芯的音叉晶体单元直径为 4.3 毫米,长度为 18.5 毫米。佩戴在手腕上时不断受到振动和物理冲击的问题通过修改晶体单元的内部结构得到了解决。
开始开发手表用CMOS IC
但是,Quartz Astron 的体积也有点大。要普及石英手表,就必须让手表和其内置的音叉晶体单元变得更小,这就意味着必须提高晶体单元的振动频率。提高振动频率本身并不困难,但这样做会增加功耗。因此,必须缩小尺寸、降低功耗并提高 IC 芯片等核心部件的耐用性。但是,当时国内没有一家制造商专门生产石英表 IC,因此,我们决定自己开发CMOS IC 并进行量产。 - 1971
-
更小、功耗更低的晶体单元的出现
适用于 Cal. 38 的音叉晶体单元
我们成功为 Cal. 38 开发出更小的音叉晶体单元。它的振动频率为 16.384 kHz,直径为 4.3 毫米,长度为 14.7 毫米。 - 1973
-
晶体单元进一步小型化,32.768 kHz成为事实上的标准振动频率
用于 Cal. 57 的音叉晶体单元
我们成功地为 Cal. 57 开发了更小的晶体单元。该晶体单元的直径为 3.9 毫米,长度为 10.9 毫米,还具有更高的振动频率:32.768 kHz。32.768 kHz 的振动频率已成为当今手表晶体谐振器的事实上的标准振动频率。 -
开发安装简便的薄型扁平音叉晶体单元
F-001平音叉晶体单元
我们还引入了扁平而非圆柱形的音叉晶体单元。晶体单元F-001晶体单元的尺寸为 5.1 毫米 x 12.1 毫米 x 2.4 毫米,比用于 Cal.F-001 的尺寸为 5.1 毫米 x 12.1 毫米 x 2.4 毫米,比用于 Cal.57 的 稍大,但却更容易装配(安装)到装有其他电子元件的印刷电路板上。圆柱形晶体元件必须垂直安装在电路板上,金属端子弯曲后平放在电路板上。相比之下,平面型只需将其插入电路板即可安装。F-001 很快就被用于价格低廉的小型手表和液晶手表中,因为它们需要在液晶面板下安装电子电路。 -
世界上第一款配备六位液晶显示屏的手表
图:Seiko Quartz 06LC
自1969年开始开发的手表用CMOS IC也于同年开始量产。
这些CMOS IC 被用于 Seiko Quartz 06LC,这是世界上第一款带有六位 LCD 显示屏的手表。 - 1975
-
光刻技术可进一步缩小元件尺寸并提高精度
当天的光刻工艺流程
光刻工艺是将沉积在晶圆上的薄金属层暴露在光线下,然后蚀刻掉不需要的区域,从而在石英晶圆上制作出微小图案的工艺。这已经是制造集成电路(IC)不可或缺的技术。光刻技术对晶体的小型化、精密化和生产化做出了巨大贡献。 -
开始销售第一批使用光刻技术生产的音叉晶体单元
C-002 是第一个使用光刻技术制造的晶体单元。
C-002 是第一个使用光刻技术制造并投入商用的晶体单元,其直径为 2 毫米,长度为 6 毫米,振动频率为 32.768 kHz。 - 1980
-
开始销售采用爱普生晶体和半导体的晶体振荡器
设立富士见工厂,致力于半导体的开发和生产。同年,公司推出了第一款晶体振荡器,该振荡器将音叉晶体单元与内部开发的手表 IC 相结合。 - 1983
-
内置晶体单元的实时时钟模块
晶体与半导体的进一步集成导致了RTC- 58321,这是一款内置晶体单元的实时时钟模块,于同年上市销售。从那时起,我们通过不断集成我们的晶体和实时时钟IC 为世界提供了各种各样的实时时钟模块,并推动了我们最初开发的技术的进步,以降低功耗并提高手表的精度。 - 1983
-
早期手机中使用的温度补偿晶体振荡器(TCXO)
肩挎式电话 - 第一代手机 - 在 1980 年代首次出现时成为热门话题。顾名思义,它们可以挂在肩上随身携带,预示着即将发生的事情:从固定电话到移动电话的过渡,最终是今天的智能手机。由于这些手机在户外和各种温度环境中使用,因此其中使用的振荡器需要在较宽的温度范围内保持频率稳定性。这种需求促使我们开发并批量生产了我们的第一款温度补偿晶体振荡器 (TCXO),这是一种体积约为 4.0 cc 的器件。爱普生一直在通过采用内部振荡电路、温度补偿电路和在光刻工艺中制造的晶体芯片来减小其 TCXO 的尺寸。今天,我们的 TCXO 的立方体积为 0.003 cc-1/1300 是我们第一台TCXO的 TCXO。 - 1984
-
SAW声表面波滤波器投放市场
单片晶体滤波器 (MCF) 是市售的,但用当时的技术很难减小石英衬底的厚度,这使得 MCF 无法应对约 70 MHz 以上的频率。然后,我们将注意力转向表面声波(SAW) 滤波器,预计可以通过缩小数字间传感器 (IDT) 之间的间距来处理更高的频率,IDT 是在石英衬底表面制造的梳状电极。MCF 原则被引入 SAW 滤波器。两个 SAW 谐振器彼此相邻放置,这两个谐振器之间的声学耦合激发了两种不同的谐振频率:f1(对应于一阶振动模式)和 f2(对应于二阶振动模式)。这两个频率用于实现与 MCF 工作原理相同的滤波器。SAW 滤波器是无线通信设备行业中一项令人兴奋的发展,因为它们可以生产出更小、更便宜的无线通信设备。
光刻技术用于 SAW 滤波器,以在石英衬底中制造 IDT。研究人员意识到,他们可以使用这项技术从石英基底上薄薄地刮下材料,并提高晶体单元和 MCF 频率。当时使用的传统机械加工技术只能生产出最高可处理约 70 MHz 的部件,但通过化学方式仅去除石英基板中心的振动部分,它们最终能够处理更高的频率。这种制造技术被称为高频基波 (HFF),后来用于高频率晶体单元和其他器件。 - 1986
-
第一个商用圆柱型 AT 晶体单元和 AT 晶体振荡器
CA-301 圆柱型 AT 切割晶体单元(3 毫米 x 8 毫米)
音叉晶体单元装配线被转移到圆柱形 AT 晶体单元的生产和商业化。CA-301 直径为 3 毫米,长度为 8 毫米,通过购买石英晶体原料和加工成石英晶片的设备实现商品化。大约在同一时间,通过将 AT 切割晶体单元和振荡 IC 在塑料模具中成型而成的 SG-51 晶体振荡器(时钟振荡器)也实现了商品化。
这两款产品的尺寸为 19.8 毫米 x 6.36 毫米 x 5.3 毫米,在小型化方面比竞争产品领先一两步。 - 1987
-
业界第一款表面贴装时钟振荡器
SG-615
该产品是为了满足当时流行的电路板表面贴装需求而开发的。传统的电路板贴装通常需要在电路板上钻孔,将元件的引线插入孔中,然后焊接到位。这种方法存在许多问题。它需要在电路板上钻通孔,这会降低电路板的强度。此外,它还耗费时间,增加了元件安装,限制了电路板的布线,降低了布线密度。相比之下,表面贴装电路板允许更大的布线自由度、更小的元件和更高的安装密度,因为元件只连接到表面。这些进步使表面贴装技术在办公设备等应用中流行起来。这也导致了 IC 等表面贴装设备 (SMD) 的出现,但金属封装的晶体设备仍然是常态。为了改变这种情况,我们开始开发晶体设备塑料封装和 SMD,这些技术充分利用了我们在半导体制造中培养的量产技术。最终的SG-615使用热固性环氧树脂作为塑料材料。振荡器内置了新开发的耐热圆柱形AT切割晶体单元,使其能够承受与表面贴装焊接工艺中使用的回流炉中的SMD IC相同的温度条件。基本输出频率范围约为1MHz至26MHz。谐波振荡允许更高阶的频率输出。通过提供允许输出信号停止和启动的输出使能功能,可以改变输出信号。此外,通过利用我们自己的CMOS IC,实现了仅25 mA的最大电流消耗。该产品开创了晶体振荡器行业向SMD转变的先河。一旦SG-615被一家美国大型计算机制造商选为PC的控制时钟,该时钟对其他PC制造商的销售量就会激增。它成为事实上的标准,产量在高峰期达到每月300万台。
- 1997
-
可编程频率晶体振荡器
SG-615
随着手机、录像机等消费类电子产品和便携式信息设备市场的扩大,产品竞争也愈演愈烈。许多制造商为了提高可用性,纷纷竞相规划和开发更小、更轻、更省电的产品。看到这种情况,为了快速响应缩短产品开发时间的需求,我们开始开发一种配备爱普生半导体芯片的晶体振荡器,该晶体振荡器可以通过编程输出所需的频率。其结果是SG-8000系列新型晶体振荡器,它基于独特的新概念。使用锁相环 (PLL) 和可编程只读存储器 (PROM) 技术,我们使用户能够使用专用写入器选择和写入所需的振荡频率、输出条件和驱动电压到组装好的振荡器。
SG-8000 系列振荡器可以通过编程输出大约 30,000 个不同的频率。它们可以覆盖市场上约80%的标准频率,使最终产品制造商只需在制作开发原型时选择程序中频率,就可以在多种不同的产品中使用它们。它们还允许接受即使是小批量的订单。此外,从收到订单到交货的时间缩短到传统产品所需时间的三分之一。这消除了按功能和频率储存晶体振荡器的需要,即使是大规模生产的产品,这反过来又减少了库存和预测订单风险。 - 2005
-
爱普生Toyocom 由 精工爱普生和 Toyocom 的晶体设备业务合并而成
精工爱普生客户主要集中在手表和消费电子应用领域领域。而东洋通信设备则专注于电信设备和工业电子设备。精工爱普生擅长光刻和微加工技术,而东洋通信设备则擅长晶体器件的基本理论。两家公司的晶体器件业务合并成立了一家新公司,爱普生东洋通信公司。
同一时期,FA-128 AT 切割晶体单元在 CEATEC JAPAN 2005 上展出。面板展示了光 AT 制造工艺,所展示的设备非常小巧,外部尺寸为 2.0 毫米 x 1.6 毫米 x 0.5 毫米。由于采用了光刻工艺,FA-128 比其前身小得多,给参观者留下了深刻的印象。 -
石英陀螺仪传感器用于数码单反相机的图像稳定应用
陀螺仪传感器负责精确检测角速率的变化,但它们需要更小、更稳定,以满足对功能性和精度更高的设备的需求。爱普生陀螺仪传感器采用石英,这是一种极其稳定的材料,其特性天生就能够在一定温度范围内保持稳定。此外,爱普生专有的光刻工艺可生产出世界上最小的陀螺仪传感器,尽管尺寸小巧,但稳定性和精度却非常出色。
其性能的秘诀在于采用光刻技术实现的独特锤头(双 T)结构。其体积小、灵敏度高,但噪音低、稳定性高。简而言之,我们的陀螺仪传感器可以安装在小型设备中,即使在恶劣的温度环境下也能提供稳定的精度。我们的石英陀螺仪传感器性能得到认可,在数码单反相机的图像稳定领域占有一席之地,并继续为汽车导航系统、车辆安全系统和其他应用中准确检测角速度变化做出贡献。 - 2009
- 爱普生Toyocom 成为精工爱普生的全资子公司。
- 2011
-
开发出世界上最小*1 IMU *2之一且功耗最低的IMU
最初,惯性测量单元 (IMU) 大多嵌入航空航天应用的专用设备中,以及其他需要高精度、稳定测量惯性测量的用途。但后来,为工业应用开发的 IMU 开始进入各种产品。新兴和不断扩展的工业应用领域需要的是提供更高精确度和稳定性、体积更小、功耗更低的 IMU,因为这些属性将使它们更容易内置到产品中。
爱普生是一家同时拥有半导体和晶体器件业务的罕见公司,它采取了独特的方法来开发 IMU。我们首先利用我们独特的技术开发了石英陀螺仪(角速率)传感器*3,以石英制造微机电系统 (MEMS),石英是一种以其出色的频率稳定性和高精度而闻名的材料。然后,我们将这些陀螺仪传感器与半导体技术和在开发 GPS 模块和其他位置信息设备时积累的专业知识相结合,完成了 IMU。凭借出色的精度和稳定性测量能力,IMU 能够准确感应惯性运动,从最轻微的倾斜到大幅度的运动。与早期的 IMU 相比,IMU 体积小、重量轻、功耗低,更容易嵌入到产品中,为产品工程师提供了更大的设计自由。工程师能够轻松地将此 IMU 嵌入到各种工业系统中,用于分析和控制惯性运动、控制移动物体、控制振动稳定性和控制导航。
*1 与工业应用中使用的其他小型 IMU 相比(根据 2011 年 5 月进行的爱普生研究)
*2 IMU 是一种用于感测惯性运动的设备。它由三轴角速率传感器和三轴加速度计组成。IMU 主要用于测量和控制移动物体的行为。
*3 陀螺仪传感器测量物体绕传感轴每单位时间的旋转角度(角速率)。 - 2012
- 爱普生Toyocom 的部分业务被拆分并被爱普生吸收。
- 2020 年后
- IoT、5G、自动驾驶etc.技术的进步和社会问题的日益严重
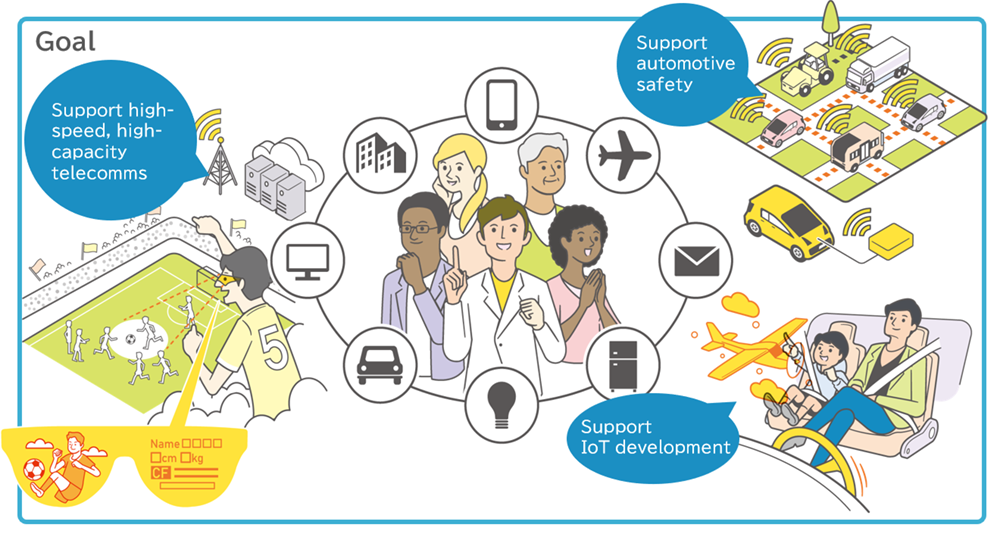
爱普生液晶器件将继续为实现智能社会做出贡献并为社会问题提供解决方案。