エプソン水晶の歴史
エプソン水晶の誕生
テレビやパソコン、腕時計などの中で静かに時を刻み続ける水晶デバイス。現在では「産業の塩」と称されるほど、エレクトロニクス業界に欠かせないデバイスへと成長しました。エプソンは、その水晶デバイスのリーディングカンパニーとして、これまで水晶デバイスの省電力化、小型化と高性能化を実現してきました。これは「省(省電力化)・小(小型化)・精(高性能化)」の合言葉でエプソンのDNAにいまも、そしてこれからも受け継がれていきます。ここでは、エプソン水晶デバイスの歴史を紹介します。
- 1891年
- 前身の事業体である「吉村商会」設立
- 1938年
- 吉村商会を継いだ東洋無線電信電話と明昭電機が合併し、「東洋通信機株式会社」設立
- 1942年
- セイコーエプソンの前身である「有限会社大和工業」設立
- 1943年
- 服部時計店のウオッチ製造部門「第二精工舎」が長野県諏訪市に疎開工場を設立
- 1959年
-
国内初の人工水晶の工業化に成功
天然の水晶は含有不純物が少なく大型で良質なものを加工して利用していたが、そのような水晶は国内で入手するのは困難だった。安定性に非常に優れた水晶は、当時世界的に軍需物資として使用されていたためである。そこで、東洋通信機株式会社は高品質で大型の人工水晶を自分たちで製造することを目指した。初めはオートクレーブの制作、高品質な人工水晶を製造するためのオートクレーブの調整、そして量産性を高めるためのオートクレーブの増設。量産をスタートさせ、国内初の人工水晶の工業化に成功した。 - 第二精工舎の諏訪疎開工場と大和工業が合併し、「諏訪精工舎」設立
- 1969年
-
世界初のクオーツ式腕時計の開発
世界初のクオーツ式腕時計
「セイコー クオーツアストロン 35SQ」水晶振動子の大きさの比較
(左側)クオーツアストロン開発前に実用化されていた水晶振動子(長さ約50mm)
(中央)クオーツアストロンに採用された音叉型水晶振動子(直径4.3mm×長さ18.5mm)それまでのクオーツ式時計といえば、精度は極めて高いものの、壁掛け時計ほどの大きさがあり、手軽に持ち運ぶことはできなかった。世界初のクオーツ式腕時計「セイコー クオーツアストロン 35SQ」を実用化させたポイントは高精度化と小型化。水晶振動子、時計用IC、小型ステッピングモータの技術により、日差0.2秒以内の高精度を実現。同時に水晶振動子の小型化に成功。従来の水晶振動子は、外形寸法が非常に大きく、腕時計に収めることは不可能だったが、この問題を「音叉型」という新しい構造を採用することで解決。
開発した水晶振動子「Cal.35SQ用」の外形寸法は、直径4.3mm×長さ18.5mm。腕に取り付けると常に振動や衝撃にさらされるという問題は、水晶振動子の内部構造を工夫することで解決した。時計用CMOSICの開発に着手
ただ、クオーツアストロンでも外形寸法は若干大きかった。クオーツ式腕時計を普及させるには、さらなる腕時計の小型化と、内蔵する音叉型水晶振動子の小型化が不可欠だと判断。そのためには振動周波数を高める必要がある。振動周波数を高めること自体は難しくないが、消費電力が増えてしまう。中枢部品の小型化、低消費電力化、耐久性の向上が必要となった。しかし当時、国内にはクオーツウオッチ専用のICを製造しているメーカーはなかったため、専用ICの自社開発を余儀なくされ、CMOSICの自社開発・自社量産を決断し、着手を開始する。 - 1971年
-
更なる小型化、低消費化を実現した水晶振動子が誕生
音叉型水晶振動子「Cal.38用」
より小型な音叉型水晶振動子「Cal.38用」の開発に成功。振動周波数が16.384kHzで、外形寸法が直径4.3mm×長さ14.7mm。 - 1973年
-
更なる小型化を追求、振動周波数32.768kHzがデファクト・スタンダード化
音叉型水晶振動子「Cal.57用」
さらなる小型の水晶振動子「Cal.57用」の開発に成功。外形寸法は直径3.9mm×長さ10.9mmで、振動周波数は32.768kHzへと高まった。なお、32.768kHzという数字は、現在の時計用水晶振動子においてデファクト・スタンダード(事実上の標準規格)になっている振動周波数となった。 -
薄型で簡易実装を可能にしたフラット型の音叉型水晶振動子の開発
フラット型の音叉型水晶振動子
「F-001」形状が円筒(シリンダー)型ではなく、フラット型の音叉型水晶振動子「F-001」も世に送り出す。外形寸法は5.1mm×12.1mm×2.4mmで、「Cal.57用」に比べると若干大きいが、電子部品を載せるプリント基板への取り付け方(実装方法)が大幅に簡単になった。シリンダー型では、水晶振動子をプリント基板に立てるように取り付け、その後に金属端子を曲げて、プリント基板の上に寝かせるという作業が必要だったが、フラット型であれば、プリント基板に差し込むだけで取り付けが完了する。普及タイプの小型腕時計や液晶パネルの下に電子回路を収めなければならない液晶ウオッチなどに相次いで採用された。 -
世界初の六桁液晶ディスプレイを搭載した腕時計の発売を開始
セイコークオーツ「06LC」
1969年に開発着手した時計用CMOS ICの量産もこの年にスタート。
世界初の六桁液晶ディスプレイを搭載した、セイコークオーツ「06LC」に搭載された。 - 1975年
-
フォトリソグラフィ技術を導入し、小型化と高精度化を目指す
フォトリソグラフィ技術のプロセス・フロー(当時)
フォトリソグラフィ技術とは、写真の露光技術を応用することで微細なパターンを作り込む技術のことだ。その当時すでに、集積回路(IC:integrated circuits)では欠かせない製造技術になっていた。フォトリソグラフィ技術を導入したことで、小型化と高精度化、生産性の向上に大きく貢献した。 -
同技術を採用後初の音叉型水晶振動子の発売を開始
フォトリソグラフィ技術で製造した最初の製品「C-002」
フォトリソグラフィ技術を採用後、初めて製品化に成功した「C-002」。
外形寸法は、直径2mm×長さ6mm。振動周波数は32.768kHz。 - 1980年
-
自社半導体技術との融合で、水晶発振器の発売を開始
半導体の自社開発・生産の本格化に向けて、富士見事業所を設立。同年、自社で開発した時計用ICと音叉型水晶振動子を組み合わせた初の水晶発振器を世に出す。 - 1983年
-
水晶振動子内蔵RTCモジュールの発売を開始
半導体技術との更なる融合により、水晶振動子内蔵のRTCモジュール「RTC-58321」が誕生し、発売を開始。そこから今も、多様なRTC ICとの組み合わせを行い、時計で培った低消費、高精度の技術を極め、多種類のRTCモジュールを世に出していく。 - 1983年
-
初代携帯電話機に温度補償型水晶発振器(TCXO)が採用
携帯電話機が世の中に登場した1980年代、「ショルダーフォン」が話題になった。その名の通り、肩に掛ける携帯電話機で、従来の固定電話機から携帯する電話への変換であった。屋外や様々な温度環境下で使用されるため、広い温度範囲においても高精度な周波数を保持できる発振器が必要となり、温度補償型水晶発振器(TCXO)を開発、量産化した。この時のTCXOは4.0ccほどの体積であった。その後、携帯電話は小型化、多機能化が著しく進化し、現在のスマートフォンに至っている。エプソンのTCXOも内部発振回路や温度補償回路のIC化、水晶チップにはフォトリソグラフィ加工を用いることで、水晶デバイスの小型化を推進。現在では、0.003ccと当時の1/1300の体積を実現している。 - 1984年
-
SAWフィルタを市場に投入
それまで市場に流れていたMCF (Monolithic Crystal Filter)フィルタだが、当時の技術では、水晶基板をそれ以上、薄く加工することが難しく、70MHz程度を超える周波数には対応できなかった。そこで、水晶基板の表面に作り込むIDT(Inter-Digital Transducer)と呼ばれる櫛歯状電極の間隔を狭くすれば高い周波数に対応できると予想し、SAW(弾性表面波)に着目。MCFの原理をSAWフィルタに持ち込むことで、二つのSAW共振子を近接配置し、二つの共振子間の音響結合により励起される異なる二つの共振周波数であるf1(1次の振動モードに対応)とf2(2次の振動モードに対応)を使ってMCFと同じ原理で機能するフィルタを実現。このSAWフィルタを採用すれば、無線通信機の外形寸法とコストを大幅に削減することが可能になるため、無線通信機業界で大きな話題となった。
SAWフィルタは、水晶基板にIDTを作り込むときに、フォトリソグラフィ技術を活用する。この技術を応用し、水晶基板を薄く削れば水晶振動子やMCFの高周波化が可能なことを見いだした。それまでの機械加工技術では70MHz程度までしか対応できなかったが、水晶基板の中央の振動部のみを化学的に削ることで、それ以上の周波数に対応することが可能になった。この製造技術を「HFF(High Frequency Fundamental)」と呼ぶ。この技術はその後、高周波の水晶振動子などに活用される。 - 1986年
-
最初のシリンダー型AT振動子、AT水晶発振器の発売を開始
シリンダー型AT振動子「CA-301」
(直径3mm×長さ8mm)AT振動子の製造に音叉型水晶振動子の組み立てラインを流用し、シリンダー型のAT振動子を製品化。水晶の原石や水晶ウェハへの加工装置は社外から購入し、音叉型水晶振動子の組み立てラインを利用することで、直径3mm×長さ8mmの「CA-301」を製品化。さらにほぼ同じタイミングで、AT振動子と発振ICを一緒にプラスチック・モールド成型した水晶発振器(クロック発振器)「SG-51」も製品化。
外形寸法は19.8mm×6.36mm×5.3mmと、いずれも競合他社品の一歩も二歩も先を行く小型化を実現していた。
写真内にある大型品は当時業界で主流だった「HC-49U」(外形寸法:幅11mm×奥行き4.7mm×高さ13.5mm)で、比較するとその小ささが分かる。 - 1987年
-
業界初の表面実装対応クロック発振器の発売を開始
SG-615
当時、普及しつつあった基板の表面実装へのニーズに応える製品として誕生。従来の基板実装は、「基板に穴をあけて、そこに部品のリード(足)を挿し込んでハンダ付けをする」という方法が一般的であったが、この方法では、プリント基板の最上部から最下部まで貫通する穴を開ける必要があり、そのために基板強度の低下や加工時間、部品実装の増加、貫通による配線の制約、配線密度の低下などの問題が起こっていた。一方、表面実装タイプの基板では、部品は表面にのみ接続されるため、配線の自由度の向上、部品の小型化、高実装密度化が可能であり、OA機器などでは表面実装が普及し始める。これに合わせ、ICなどでは表面実装部品(SMD)が生まれてきたが、水晶デバイスはまだメタルパッケージが主流。そこで当社は、半導体製造で培った量産技術をベースに水晶デバイスのプラスチックパッケージ化、SMD化に取り組んだ。その結果誕生した「SG-615」は、プラスチック素材に熱硬化性のエポキシ樹脂を使用。表面実装のハンダ付け工程で使用されるリフロー炉の温度条件にも耐えられるよう、新たに開発した耐熱シリンダー型AT振動子を内蔵し、汎用SMDICと同等のハンダ付温度条件を実現。基本出力周波数範囲は、約1MHz〜26MHz。オーバートーン発振でさらに高次の周波数出力も可能。さらに、出力信号を止めたり出したりすることができるアウトプットイネーブル機能を備え、出力信号を変化させることができた。また、自社製CMOSICの強みを生かし、最大でも25mAという低消費電流を実現。この製品が水晶発振器業界のSMD化への先鞭を切ることとなった。「SG-615」は米大手コンピュータメーカーのパーソナルコンピュータ用制御クロックとして採用されると、瞬く間に各社のPC用クロックとして販売が急増。ピーク時には月産300万個をも記録するデファクト・スタンダード製品となった。
- 1997年
-
プログラマブル高周波水晶発振器の発売を開始
SG-615
携帯電話、VTRムービー等の民生機器や携帯情報機器の市場拡大に伴い、商品競争が激化する中、多くのメーカーでは使いやすさ向上のため、各製品において小型化・軽量化・省電力化を図る商品企画・開発にしのぎを削っていた。そこに着目した当社は、市場の激化に伴う「商品開発期間短縮化」のニーズに素早く対応できるよう、グループの半導体技術を活かしながら、プログラムすることで任意の出力周波数を設定できる水晶発振器の開発に着手。
PLL(Phase Locked Loop:位相同期系)とPROM(Programmable Read Only Memory)技術を使用し、組み立て済みの発振器に対し、専用ライタで必要な発振周波数、出力条件、駆動電圧を選択して書き込むことができるという、他に類を見ない新発想の水晶発振器を開発。この「SG-8000シリーズ」は、約3万種の周波数をプログラムによって作り出すことが可能。その結果、市場で標準的に使われる周波数の約80%をカバーできることになり、セットメーカーが開発試作を行う際に、プログラム上で周波数を選択するだけで複数の異なる商品に適用することが可能となり、少量のオーダーにも対応。さらに、受注から納入までにかかる期間を、従来品の1/3に短縮することに成功。これにより、量産品についても機能・周波数別に水晶発振器の在庫を持つ必要がなく、在庫リスク・見込み発注リスクを軽減できるようになった。
- 2005年
-
東洋通信機とセイコーエプソンの水晶デバイス事業が統合し、「エプソントヨコム株式会社」設立
セイコーエプソンが守備範囲とする顧客は時計や民生機器。一方、東洋通信機は通信機器や産業用電子機器。技術については、セイコーエプソンは、フォトリソグラフィ技術や微細加工技術を得意としており、東洋通信機は水晶デバイスの基礎理論に精通していた。新会社の社名は「エプソントヨコム株式会社」。
同じ時期、出展した「CEATEC JAPAN 2005」では、ATカット水晶振動子「FA-128」を展示。フォトATの製造プロセスを紹介するパネルと、外形寸法2.0mm×1.6mm×0.5mmの非常に小さいデバイス。フォトリソグラフィ技術を利用することで、従来品に比べて大幅な小型化を実現した。来場者に大きなインパクトを与えた。 -
デジタル一眼レフカメラの手振れ補正用途に水晶ジャイロセンサーが採用
機器の高機能化・高精度化の要求から、角速度変化の正確な検知を担うジャイロセンサーは、より小さく高安定へと進化する必要があった。エプソンの水晶ジャイロセンサーは、生まれながらに温度の変化による影響を受けにくい特性を持つ「水晶」を素材としていることに加え、独自のフォトリソグラフィ加工技術を用いて、安定度、高精度、世界最小クラスを実現した。
その高性能の秘密はフォトリソグラフィ加工技術により実現した独自のダブルT型構造です。小型・高安定ながら、低ノイズ、高感度を実現。つまり小型の機器にも搭載でき、過酷な温度環境のなかでもいつでも変わらぬ安定した精度を発揮する。水晶ジャイロの性能の良さが認められ、デジタル一眼レフカメラの手振れ補正用に採用、カーナビ、車載セーフティ等でも正確な角速度変化の検知に貢献し続けている。 - 2009年
- セイコーエプソンによる完全子会社化
- 2011年
-
世界最小クラス※1の外形サイズ・消費電力を実現した慣性計測ユニット※2(IMU)開発
当初、IMUは慣性運動について高精度・高安定な計測が必要な航空・宇宙分野などで、専用機器に組み込まれ利用されることが一般的であったが、その後産業・工業分野向けのIMUも開発され、さまざまな製品への組み込みが進み、市場の拡大が見込まれていた。この新しい市場で求められていたのは、IMUの製品への組み込みを容易にするために、精度や安定性を高めながら、さらなる小型化と低消費電力化を実現すること。
水晶デバイス事業と半導体事業の両方を展開する稀有な企業であるエプソンは、高精度・高安定などの優れた特性を持つ素材である水晶に、精密微細加工を施す独自の水晶微細加工技術を用い、水晶ジャイロ(角速度)センサー※3を開発。それに、GPSなど位置情報デバイスで培った半導体技術やノウハウを融合させるという独自のアプローチで、この製品を誕生させた。高精度・高安定な計測性能をもち、わずかな傾きから大きな動きまで、慣性運動情報を正確に検出することが可能。小型・軽量・低消費電力のため、従来のIMUより組み込む製品の設計自由度が高く、さらに、慣性運動の解析・制御、モーション解析・制御、移動体制御、振動制御・安定化、ナビゲーションシステムなど、それまで難しかったさまざまな産業・工業分野の製品への組み込みを可能にした。
※1 従来の産業、工業分野向け小型IMU製品との比較(2011年5月末時点、エプソン調べ)
※2 3軸の角速度センサーと3軸の加速度センサーからなる慣性運動量を検出する装置。主に運動体の挙動の計測、制御を目的として使用
※3 検出軸まわりの単位時間当たりの回転角度(角速度)を検出するセンサー - 2012年
- エプソントヨコムを吸収分割
- 2020年以降
- IoT、5G、自動運転などの進展、社会課題の深刻化
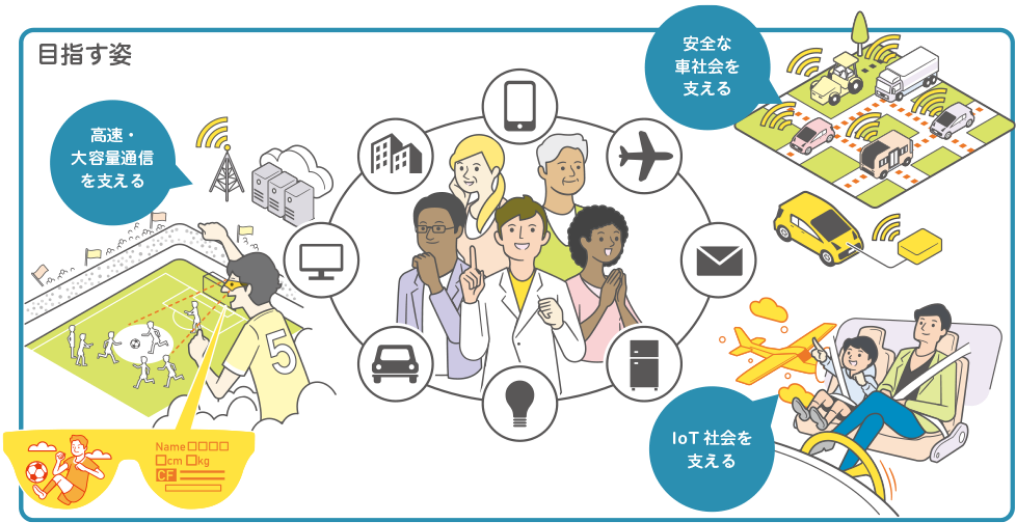
エプソンの水晶デバイスは、スマート化する社会の実現と
社会課題解決に引き続き貢献していきます。